【简答题】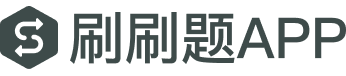
连续操作釜式反应器的热稳定条件是Qr=Qc,且dQr/dT 对于n>0的简单反应,各反应器的生产能力大小为:PFR最小,N—CSTR次之,1一CSTR最大。 单一反应过程,采用平推流反应器总比全混流反应器所需要的体积小。 固定床反应器的传热速率比流化床反应器的传热速率快。 固定床反应器比流化床反应器的传热效率低。 对于列管式固定床反应器,当反应温度为280°C时可选用导生油作热载体。 流化床反应器的操作速度一定要小于流化速度。 选择反应器要从满足工艺要求出发,并结合各类反应器的性能和特点来确定。 生产合成氨、甲醛反应器属于固定床反应器。 苯烃化制乙苯,乙醛氧化合成醋酸,乙烯直接氧化生产乙醛都可选用鼓泡塔反应器. 化工基础数据可分为两类:物性数据和热力学数据。 反应物的单程转化率总小于总转化率。 从经济观点看,提高总转化率比提高单程转化率更有利。 空速大,接触时间短;空速小,接触时间长。 化学反应器的空时就是反应物料在反应器内的停留时间,用来表明反应时间长短。 原料消耗定额的高低,说明生产水平的高低和操作技术水平的好坏。 实际过程的原料消耗量有可能低于理论消耗定额。 原料纯度越高,原料的消耗定额就会越低。 两套合成氨生产装置生产能力均为600kt/a,说明两套装置具有相同的生产强度。 提高设备的生产强度,可以实现在同一设备中生产出更多的产品,进而提高设备的生产能力。 利用苯作为原料生产某一有机化合物,平均月产量1000t,月消耗苯1100t,苯的消耗额为1.1t苯/t产品。 化工产品生产中,若每小时投入的某种原料量增加10%,结果发现单程收率不变,说明作为计算基准的该原料量增加10%。 乙酸乙烯酯的合成,乙炔气相法的时空收率为1t/(d·m3催化剂),乙烯气相法的为6t/(d·m3催化剂),说明乙烯气相法设备的生产强度较乙炔法的高。 已知通入苯乙烯反应器的原料乙苯量为1000kg/h,苯乙烯收率为40%,以反应乙苯计的苯乙烯选择性为90%。原料乙苯中含甲苯2%(质量分数),则每小时参加反应的乙苯量为435kg。 采用列管式固定床反应器生产氯乙烯,使用相同类型的催化剂,在两台反应器生产能力相同条件下,则催化剂装填量越多的反应器生产强度越大。 反应与分离过程一体化,如反应一精馏、反应一吸收等,能提高可逆反应效率。 按照原理,化工生产过程由三种基本传递过程和反应过程组成。 若该化学反应既是放热又是体积缩小的反应,那么提高压力或降低温度均有利反应的进行。 根据可逆变换反应式CO+H2 O—一C02+H2,反应前后气体体积不变,则增加压力对该反应平衡无影响,因此变换反应过程应在常压下进行。 对于连串反应,若目的产物是中间产物,则反应物转化率越高,其目的产物的选择性越低。 平行反应,若主反应活化能大于副反应活化能,则升高温度有利于提高选择性。 根据反应平衡理论,对可逆反应,随转化率的升高,反应温度应逐渐降低。 工业合成氨的反应是放热过程,随着瞬时转化率的增加,最适宜温度是降低的。 动力学分析只涉及反应过程的始态和终态,不涉及中间过程。 延长停留时间可以使原料的转化率增加,选择性下降。 在实际生产中,采取物料的循环是提高原料利用率的有效方法。 对于化工生产过程中混合气体的压缩输送过程,若其压缩比大于4~6时,则必须采用多级压缩。 从理论上说,多级压缩的级数越多压缩的终温越低。 对于合成氨中一氧化碳变换反应,存在着一个最佳反应温度。 一氧化碳变换反应是一个可逆的体积减小的放热反应,故提高压力和降低温度均可提高一氧化碳的平衡转化率。 在合成氨反应中,增大反应物浓度,反应物的转化率一定提高。 在氨合成塔中,提高氨净值的途径有:升高温度,提高压力,保持氢氮比为3左右并减少惰性气体含量。 硫氧化物的控制技术和工艺可分为燃烧前脱硫与燃烧后脱硫两大类型。 氨氧化法制硝酸时,降低温度、提高压力,可以提高一氧化氮的氧化率。 煤水蒸气转化法制氢工艺中,水蒸气分解率代表水蒸气与碳的反应程度。 在尿素的生产工艺中,提高氨碳比,能防止缩二脲的生成,保证产品质量,同时减轻甲铵液对设备的腐蚀。 鲁姆斯裂解乙烯装置急冷系统采用先水冷后油冷。 管式裂解炉最易结焦的部位是出口处和弯头处。 尾气中的H2S气体可选用二乙醇胺吸收。 高压法甲醇合成塔的原料气分主、副线进料,其中副线进料的目的是调节原料气的浓度。 乙醛氧化制醋酸,反应压力愈高愈好,因此宜采用很高的压力条件。 乙烯高压法中的聚合反应属于自由基型的聚合反应。 聚合物的熔融指数指在一定温度、压力条件下,聚合物经过一定长度、一定直径的毛细管,在5min内流出的物料量(以克计)。 聚氯乙烯在工业上的生产方法主要是乳液聚合。 聚氯乙烯树脂都是由氯乙烯单体经自由基聚合反应合成的。其工业生产方法主要为本体聚合法。 聚合反应中,氮气常用于置换反应装置和输送催化剂等多种用途。 聚甲基丙烯的聚合反应属于自由基型聚合反应。 多元醇和多元酸经缩聚反应可生产聚氨酯。 在乳液聚合中,乳化剂不参加聚合反应,但它的存在对聚合反应(聚合反应速率和聚合物的相对分子质量)有很大影响。 由生胶制造各种橡胶制品一般生产过程包括塑炼、混炼、压延、成型、硫化个阶段。 未经硫化的橡胶分子结构是线型或支链型,硫化的目的是使橡胶分子适度交联,形成体型或网状结构。 橡胶成型的基本过程包括:塑炼、混炼、压延和挤出、成型和硫化等基本工序。 塑炼是指将橡胶由高弹态转变为可塑状态的过程。 悬浮聚合可以近似认为是由无数个小本体聚合组成的。 本体聚合的关键问题是聚合热的排除。 在合成橡胶中,弹性最好的是顺丁橡胶。 在缩聚反应过程中不会生成低分子副产物。 悬浮聚合体系一般由单体、水、分散剂、引发剂组成。 酚醛树脂、醇酸树脂、聚酰胺属于缩聚物有机高分子化合物。 若想增大丁苯橡胶的刚性,可增大苯乙烯的比例。 对气一固催化反应,工业上为了减小系统阻力,常常采用较低的操作气速。 催化剂使用初期活性较高,操作温度宜控制在工艺允许范围内的较低处。 液相本体法生产聚丙烯的投料顺序为:第一步投底料,第二步投活化剂,第三步加催化剂,第四步加氢气。 固定床反应器操作中,对于空速的操作原则是先提温后提空速。 渣油催化裂化的一个显著特点是高温短停留时间。 流化床中料腿的作用是输送旋风分离器分离下来的催化剂粉尘并起密封作用。 催化剂颗粒越大,旋风分离器回收效率越低。 对于同类烃,其相对分子质量越大,发生催化裂解反应的速率越慢。 在裂化过程中生成的焦炭并不是纯碳,而是脱氧缩合生成的一种碳氢比很高的稠环芳烃。 决定烃类催化裂化反应速率快慢的关键是化学反应。 反应温度提高后,柴油的十六烷值降低,胶质含量增加。 对于再生器烧焦过程来说,供氧必须和需氧相等才能达到平衡。 进入旋风分离器锥体的催化剂速度会越来越慢,最后进入料斗,经料腿排入床层。 对于氮、硫含量较高的原料,可通过加氢精制的方法进行脱硫脱氮预处理。 提高反应温度能提高汽油辛烷值,因为汽油中的烯烃都随温度提高而增加。 固体颗粒能够被比自己轻得多的流体流化起来,其内在原因是流体在颗粒固体之间流动时与小颗粒产生摩擦力。 实际生产中高线速的气体流化床因为气泡的存在流化并不均匀,床层的压力降是在变化的。 催化裂化流化床易于散式流化。 测定聚丙烯的特性黏度便可知聚丙烯的平均相对分子质量。 空气不可作为气态润滑剂。 润滑油黏度的表示法分两类:绝对黏度和相对黏度。 抗乳化度好的润滑油,油与水不能生成稳定的乳化液,可以很快分离。 从热力学角度考虑,提高反应温度有利于一次反应和二次反应的进行。 重质原油在低温条件下有利于油水分离。 燃料高热值减去低热值就是水蒸气的相变热。 抗氧化剂又称防胶剂,它的作用是抑制燃料氧化变质进而生成胶质,提高柴油的安定性。 油品的动力黏度是指油品内分子之间因运动摩擦而产生的阻力大小。 碱性氮是油品氮化物中最难被加氢,而使N转化成NH。的物质。 碱性氮在精制油中含量的高低反映了油品加氢精制的深度。 在事故处理时,吹扫用的氮气纯度必须>99.9%。 注水采用的是无盐水。 胺的贮罐及缓冲罐用氮气保护,可以减少氧化而变质。 在脱硫操作中,压力高能够延长气体与脱硫剂接触时间,提高脱硫效果。 甲烷化反应剧烈放热,易造成超温。 只要氢分压足够高,加氢裂化过程不会有脱氢反应发生。 所有可以和氢气反应生成硫化氢的硫化物都可以用作硫化剂。 二甲基二硫化物(DMDS)是目前使用较多的硫化剂。 用甲基二乙醇胺作脱硫剂,不仅能脱除硫化氢,还能脱除COS、RSH、二硫化碳。 加氢裂化过程有水生成,所以原料含水并不重要。 使用1.0MPa、250°C的饱和蒸汽作热源,脱硫剂会分解、老化,所以不合适。 压力越低越有利于裂解反应的进行。 低温时油水分离不好,因此,为使油水分离,温度越高越好。 非烃化合物是指所有的除含有C、H元素以外,还含有其他元素的有机化合物。 含硫化合物加氢后有硫化氢生成。 甲烷化反应生成的是甲烷,不会影响产品的质量,也不影响催化剂的活性和寿命,所以氢中含有多少一氧化碳和二氧化碳没关系。 因为加氢裂化使用的催化剂必须在硫化态时才有活性,因此原料中的硫含量越高越好。 过剩空气系数越大,越能保证燃料的充分燃烧,加热炉的热效率也越高。 催化剂的空速越小,油品与催化剂接触的时间越长。 装置升温升压后,如没有可燃气体检测仪,也可以用肥皂水继续查漏点。 加氢裂化过程是一个放热反应过程,因此降低反应温度反应深度增大。 乙醇胺是一种脱硫剂,也是一种弱碱,碱性随温度上升而减弱。 我国生产的航空汽油是催化裂化或催化重整所得的低辛烷值汽油馏分。 只有当温度<230°C就可以和氢气反应生成硫化氢的硫化物,才能作为硫化剂使用。 含硫化合物的腐蚀只有在较高的温度下才会产生。 在一定温度、压力下,脱硫剂的化学吸收脱硫,溶解度是一定的。 当石油馏分沸程相同时,含芳烃越多密度越大,‘含烷烃越多密度越小,所以可通过密度值大致看出油品中烃类组成。 加氢裂化过程氢分压越高越好。 加氢裂化过程操作压力越高越好。 在实际生产中,改变空速和改变温度一样也可以调节加氢裂化产品的分布。 加氢裂化过程各类反应进行的深度不受工艺条件的影响。 因为氢气不会结焦,因此,只要材质允许,可以将氢气加热至任意高的温度。 加热炉热效率越高,燃料的利用率越高,燃料消耗越低。 惰性气体进入系统后也不会发生化学反应,氢气中惰性气体的含量可以不控制。 乙烯装置生产具有高温、高压、深度冷冻的特点,同时又有硫、碱等腐蚀介质的存在,所以单台裂解炉的开工率是指年实际开工日数与年设计运行日数之比。 当原料油品质变化时,应根据原料油品质的变化对裂解炉操作条件和急冷系统进行及时调整。 管式裂解炉冬季停用炉内保持一定数量的火嘴处于燃烧状态是为了防止炉管低温腐蚀。 当裂解炉的炉型确定后,裂解原料组分变化对炉出口温度没有影响。 裂解气中炔烃的含量与裂解原料和操作条件有关,对于一定的裂解原料而言,炔烃的含量随裂解深度的提高而减少。 在裂解气压缩过程中,除去了裂解气中全部的水和重烃。 对于裂解气酸性气体的碱洗来说,碱浓度越高越好。 裂解气深冷分离过程中,脱除裂解气中的水分采用精馏法。 分子筛吸附水汽的容量随温度的升高而升高。 完成干燥作业的首要条件是根据被干燥系统对干燥后的要求,结合装置工艺和设备现状选定或配置供系统干燥作业的低的连续气源。 干燥器的再生原理是分子筛在高压低温状态下对脱附水有利。 裂解气的深冷分离原理是在低温条件下,将氢及甲烷以上更重的烃都冷凝下来,然后利用各烃的相对挥发度的差异,在精馏塔内进行多组分的分离,最后再利用精馏得到高纯度的乙烯、丙烯及其他烃类。 在深冷分离过程中,由于温度极低,极易散冷,用绝热材料将高效换热器和气液分离罐等都包在一个箱子里,这个箱子称为冷箱。 节流原理是根据焦耳一汤姆逊效应,即气体物质在其转化温度以下,绝热膨胀,使自身温度下降,且相同条件下同一种物质在节流前后,压力降越大,温度差也.越大。 在相同条件下,同种物料在节流前温度越低,则节流后的温度越低。 乙烯装置采用混合冷剂制冷循环(即多元制冷)不仅可以节约能量,而且可以节省设备投资费用。 采用两种或多种不同的冷冻剂进行并联操作,组成复叠式制冷压缩机的制冷过程,为复叠制冷。 甲烷化反应是氢气中的一氧化碳与氢气在镍型催化剂作用下反应生成甲烷和水的过程。 裂解气深冷分离过程中,脱除炔烃常用催化加氢法。 由热力学可知,催化加氢反应平衡常数随温度的升高而变大,所以提高温度对反应平衡有利,但温度过高容易造成飞温,所以要适当选择反应温度。 乙炔加氢过程中形成的乙烯、乙炔二聚、三聚的低聚物,是褐绿色透明状液体,称为绿油。 飞温是在很短的时间内,床层局部温度急剧上升的现象。 火炬最大排放量的确定原则是按事故状态时各系统排出的全部气体总量来考虑的。 火炬正常燃烧时,分子封氮气应该关闭。 火炬点火前,要确认其他装置与火炬相连的所有系统与大气隔断,其火炬排放管线及火炬常明线管线已用氮气彻底置换合格。 联动试车的目的是全面考核全系统的设备、自控仪表、联锁、管道、阀门和供电等的性能与质量,全面检查施工安装是否符合设计与标准规范要求。 联动试车阶段包括全系统的气密、干燥、置换、三剂填充,一个系统的水运、油运和运用假物料或实物料进行的“逆式开车”。 单机试车由设计单位负责编制方案并组织实施,施工单位参加。 乙烯装置开车方案优化的目的是在安全的基础上,争取在最短时间内取得合格产品,以较低的试车费用获得最佳的经济效果。 管道系统的吹扫目的是将系统存在的脏物、泥沙、焊渣、锈皮及其他机械杂质,在化工投料前彻底吹扫干净,防止因管道及系统存有杂物堵塞阀门、管道及设备,发生意外故障。 装置正常停车前,应根据装置运转情况和以往的停车经验,在确保装置安全、环保并尽量减少物料损失的情况下停车,并且尽量回收合格产品,缩短停车时间。 局部紧急停车的特点就是能在短时间内恢复装置开车,处理的原则是各系统能保持原始状态的就尽量维持。 在处理局部停车时要注意停车部分与全装置各系统的联系,以免干扰其余部分的正常运转而造成不必要的损失。
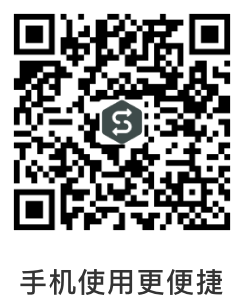

手机使用

分享

复制链接

新浪微博

分享QQ

微信扫一扫
微信内点击右上角“…”即可分享

反馈

收藏

举报
参考答案:
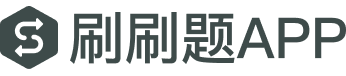
参考解析:
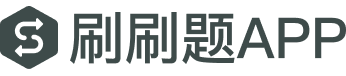